Achieving the tightest tolerances possible has and always will be our highest priority. Our dialed in, straightforward manufacturing protocols foster unquestionable repeatability. For example, throughout the entire multi-step process, Oliver’s connecting rods are constantly tested against the same three reference points, known as datums A, B, and C. These three points serve as the foundation upon which every single part at Oliver is manufactured. The utilization of premium materials, cutting edge measurement techniques, top of the line quality control, and extreme attention to detail is proof of our unwavering commitment to a finished product we stand behind, every single time. At Oliver we are striving to erase even the smallest traces of variation in our racing parts altogether.
Every manufacturing operation we perform revolves around a specific control processing technique called Geometric Dimensioning and Tolerancing (GD&T)
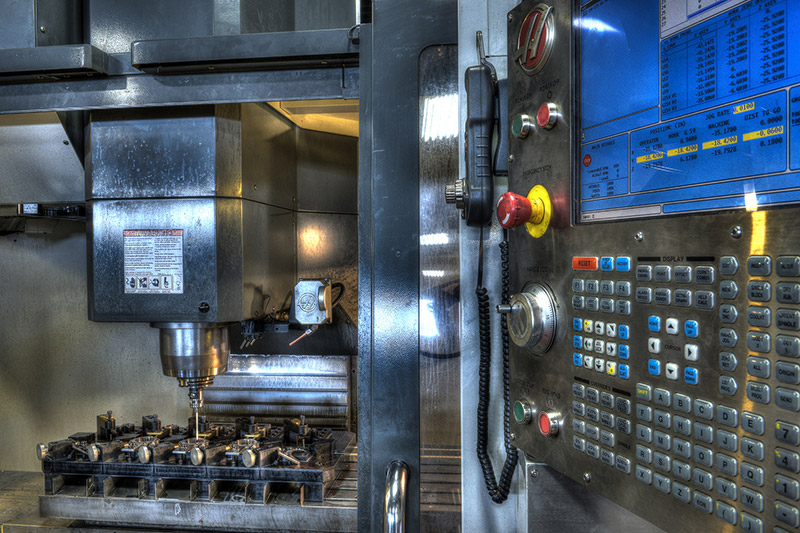
GD&T serves as the cornerstone of Oliver’s commitment to provide championship winning racers with the highest quality connecting rods. Control drawings that govern key dimensioning and tolerancing, fixtures that locate off key Datum points, and our state of the art climate controlled facility ensure Oliver’s machining and measurements are absolutely repeatable. Oliver implements the same elite processes used by the world’s top tier precision machining companies. Our Zeiss CMM and Sunnen SH4000 electro servo honing machine demonstrate our commitment to invest in the latest, most advanced technologies, undoubtedly placing us at forefront of the racing industry.
Oliver is devoted to extracting every last benefit from our U.S. alloy steel for our racers. From the very start of production, our material is processed using a higher standard for cleanliness and purity, meeting AMS 2301. Our proprietary two stage heat treatment optimizes stress relief and provides superior grain structure and ideal grain size. We continuously strive to give our racers the “unfair” advantage. Oliver rods are better by design.
Craftsmanship • Precision • Durability • Strength.
About Our Products
Oliver Rods are Better By Design™
Oliver I-beam connecting rods feature our exclusive “Parabolic Beam®” design that reduces beam stress and delivers the highest strength to weight ratio of any connecting rod currently made.
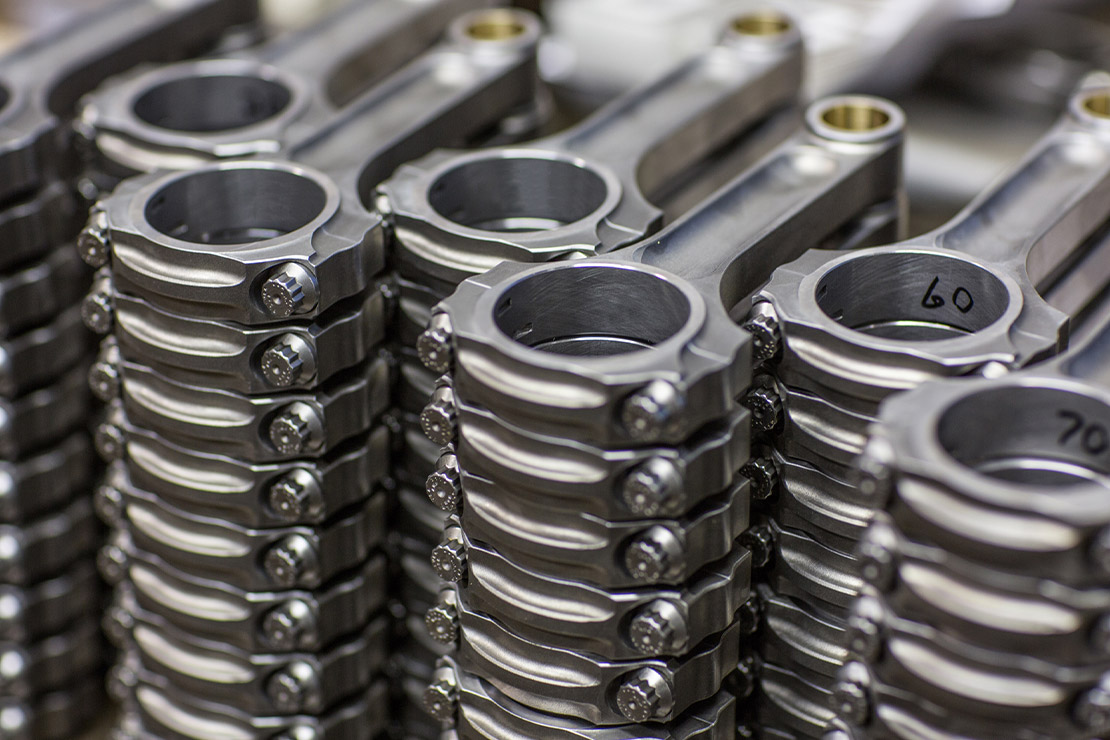
Our Standard Light rods have been designed for the heart of the racing engine category. These rods represent the perfect balance between weight and strength. In applications where weight is the primary concern we offer our Ultra Light series. For those of you pushing beyond the limits where weight takes a back seat to absolute strength, our Speedway and Max series rods are the only answer. For the most powerful engine builds you will want to spec in our Max Plus rods.
All Oliver rods are precision machined using only premium mill certified aircraft quality E4340 AQ chromoly alloy, heat treated to produce 100% martensite grain structure.
“Parabolic Beam®” is a registered trademark of Oliver Racing Parts, Inc.
ZEISS Coordinate Measuring Machine (CMM)
The ZEISS CMM provides ultimate dimensional information directly on the production line. The temperature control on our shop floor makes it possible for the ZEISS CMM to perform within the actual production line through the facility’s tightly controlled atmospheric pressure and climate. This elite machine offers maximum efficiency when it comes to in production waiting times, but quality control remains our top priority. Most importantly, the ZEISS CMM establishes reliable reproducibility through top of the line software and technology, erasing any uncertainty or fluctuations as a result of outdated manual measuring techniques.
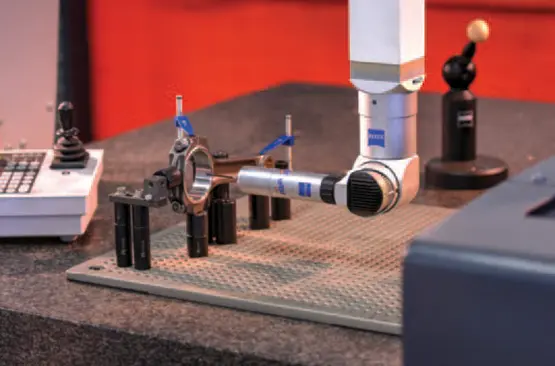
Sunnen Hone
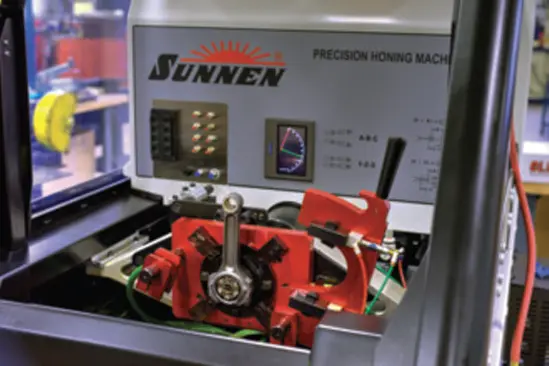
Designed to achieve exceptional finish quality, the Sunnen Hone SH-4000 is the next generation of power stroke honing machines. With 45 percent fewer parts and greater reliability than its mechanical predecessors, the SH-4000 introduces patent pending digital servo tool feed and cutting pressure control for consistent, predictable performance with micron tolerances. By controlling parallelism and concentricity leading up to the final honing operation, less demand is placed on the honing operation, giving Oliver the ability to maintain optimum surface finish characteristics. Less stock removal, combined with improved parallelism and concentricity reduces the need for adjustments, ultimately leading to better tooling life throughout the honing process.
Air Gauge
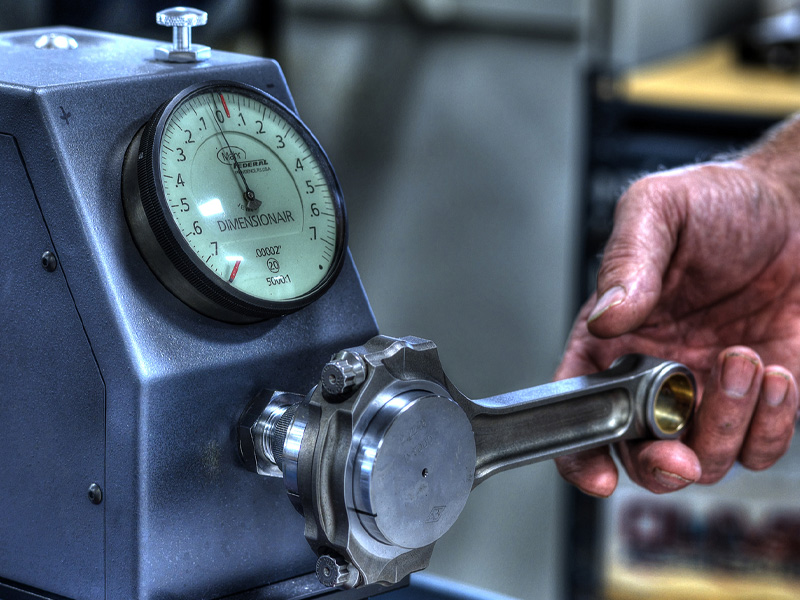
Working with the tightest of tolerances, air gauging as a measurement method is critical to Oliver’s accurate high volume manufacturing process. Parallelism and concentricity implemented prior to the hone operation opens up the potential for extremely consistent bores for the gauging of the part. With only .002 travel and a measurement tolerance of .00002, our gauges offer the ability to control the part and therefore, give us authority over the entire gauging process. Lastly, we run the air through a dryer and two micron filters to generate consistent dry air for every single measurement. When measuring rod diameters down to the most extremely precise points, air gauges are not only one of the most elite choices, but they also take out any chance of a flawed or limited mechanical instrument entirely.
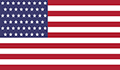
The meaning of Made in America
Oliver connecting rods are made in America, from 100%American materials by the finest craftsmen in the world: Americans. Throughout our catalog we proudly display the American flag and use the term “Made in America” in honor of that commitment.
For generations, “Made in America” has signified the quality, durability and innovation of the product that bore the mark. We believe that is still true today.
Our success is the result of years of continuous product development. Our rod designs have been refined with feedback from the world’s best engine builders racing everywhere from the biggest NASCAR venues to local dirt tracks all over the U.S. and around the world. Our experience cannot be copied. Our knowledge of what works and what does not is without equal.
We do not and will not cut corners. We utilize the best materials from the finest suppliers. We use best practices in design and manufacturing. Each and every Oliver rod is built with Craftsmanship, Precision, Durability and Strength.
The fact is, we build what are arguably the best connecting rods in the world using American craftsmen and American materials. Oliver connecting rods are proudly, “Made in America.”